Manifold switchover for gas, high quality, safety
Manifold switchover for gas oxygen, nitrogen, argon, helium, hydrogen, CO2…
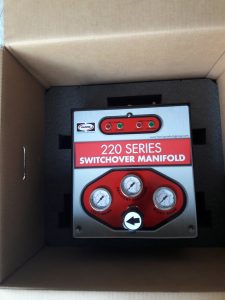
- Industrial distribution
- shipyard
- Mild steel
The Model 220 switchover manifold
- Designed to provide a continuous supply of gas
- The system automatically changes from a depleted bank of cylinders in service to the full reserve bank without an interruption of gas supply
- The standard outlet regulator maintains a constant line pressure, even during the switchover process
Design specifications model 220
- Maximum inlet pressure 3000 psi ( 400 psi for Acetylen, LPG)
- Pressure gauge size 2”
- Inlet connection 1/2” FNPT port
- Outlet connection 1/2” FNPT port
- Alarm : integral for non-flammable gas systems, optional remote alarm available for all systems
- Header 1/2” nominal pipe size
Instructions manifold switchover
1. Remove the front cover of the manifold control box with a Fillips Head screwdriver
2. Using a 5/32” Allen Hex key, loosen or remove the set screw of the top delivery pressure regulator. This regulator will be reset to the desired pressure later
3. If equipped, close the master shut off valves for both the right and left side . Refer to Figure 5 for the location of the master shut off valves
4. Turn the selector knob on the control box to the primary side (right or left)
5. S-L-O-W-L-Y open the first cylinder valve on the primary side. Warning: it is important that all cylinder valves be opened slowly to minimize the heat of recompression, which can create hazardous situations with high pressure oxidizing gases
6. Check for leaks of both ends of the hose, at the cylinder and also at the header bar. Use the soapy water solution or any oxygen compatible commercial leak detector to check for leaks. If leaks are found, they must be eliminated before proceeding. Attempt to re-tighten connection with a wrench until the leakage stops. If leakage cannot be stopped, do not use the manifold. Contact the Harris Products Group, or your local gas supplier
7. Once all leaks are eliminated, proceed to open up all cylinders on the primary side repeating step 5 and 6 for each one
8. Proceed to open up all cylinders on the reserve or secondary side repeating steps 5 and 6 for each one
9. If equipped, S-L-O-W-L-Y open the master shut off valve on the primary side and check for leaks where the header bar attaches to the control box using soapy water or commercial leaks detector at step 6. Eliminated any leaks found
10. Repeat step 7 for the reserve or secondary side
11. Check to insure that both the Right bank gauge and left bank gauge read the proper pressure from the cylinders
12. With the right bank and left bank now open, the primary knob turned to indicated the primary bank, adjust the delivery pressure to achieve the desired pipeline pressure using the 5/32” Allen Hex Key. Rotate the adjusting screw clockwise until the desired pressure is read on the delivery pressure gauge. It may take a few seconds for the pressure to equalize in the downstream pipeline
13. Once the desired pipeline pressure has been achieved, re-assemble the front cover using the Fillips Head Screwdriver
14. Non-flammable gas systems will come with a power supply and integral alarm. Plug the power supply cable into the bottom connector on the control box and the other and into a 120VAC electrical outlet. The status lights on the front of the box should be green (normal) on both sides. When the primary side is depleted, the system will change over to the reserve or secondary side and the primary side light will go from green (normal) to red (empty)
Please contact for more information : 0913997768 (call/zalo/viber)